模具维修成本降低步骤:技术创新与精细管理并行
随着制造业的快速发展,模具作为工业生产中的关键部件,其维修成本的高低直接影响到企业的经济效益。降低模具维修成本,提高生产效率,已成为企业提升竞争力的迫切需求。本文将结合降低模具维修成本报告,从技术创新和精细管理两方面探讨如何有效降低模具维修成本,以期为企业提供有益的参考。
一、技术创新,提升模具使用寿命
1. 材料创新
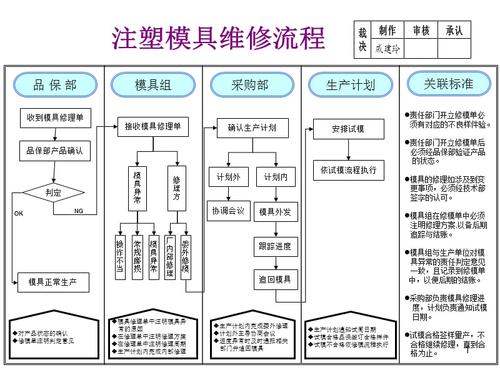
模具材料是影响模具使用寿命的关键因素。选用高性能、耐磨损、易加工的模具材料,可以有效降低维修成本。近年来,我国在模具材料领域取得了显著成果,如高温合金、高速钢、高锰钢等新型模具材料的应用,大幅提升了模具的耐磨性和使用寿命。
2. 设计创新
优化模具结构设计,提高模具的稳定性和耐用性,是降低维修成本的重要途径。通过采用模块化设计、简化结构、减少加工难度等手段,降低模具的制造成本和维修难度。运用计算机辅助设计(CAD)和计算机辅助工程(CAE)等技术,对模具进行精确模拟和优化,提高模具的可靠性和使用寿命。
3. 制造工艺创新
采用先进的制造工艺,如精密加工、激光切割、电火花加工等,可以提高模具的加工精度和表面质量,减少维修次数。采用绿色制造技术,如清洁生产、节能降耗等,也有利于降低模具维修成本。
二、精细管理,优化维修流程
1. 建立模具维修管理制度
制定完善的模具维修管理制度,明确维修流程、责任分工、验收标准等,确保模具维修工作有序进行。加强维修人员培训,提高维修技能,降低维修成本。
2. 实施预防性维修
预防性维修是一种基于对模具运行状态的预测和评估,提前采取措施防止故障发生的方法。通过定期检查、维护和保养,减少模具故障发生的概率,降低维修成本。
3. 优化维修资源
整合维修资源,实现资源共享,降低维修成本。如建立模具维修数据库,收集、整理维修案例,为维修工作提供参考;优化维修设备配置,提高维修效率。
4. 加强供应商管理
与模具供应商建立长期合作关系,选择优质供应商,降低采购成本。对供应商进行质量考核,确保模具零部件质量,减少维修成本。
降低模具维修成本是企业提高经济效益的重要途径。通过技术创新和精细管理,可以从材料、设计、制造工艺、维修流程等方面入手,有效降低模具维修成本。企业应根据自身实际情况,制定合理的降低模具维修成本策略,以实现可持续发展。
引用权威资料:《中国模具工业年鉴》显示,我国模具行业维修成本占总成本的30%以上,降低模具维修成本具有显著的经济效益。在当前市场竞争激烈的环境下,企业应积极采取措施,降低模具维修成本,提高市场竞争力。